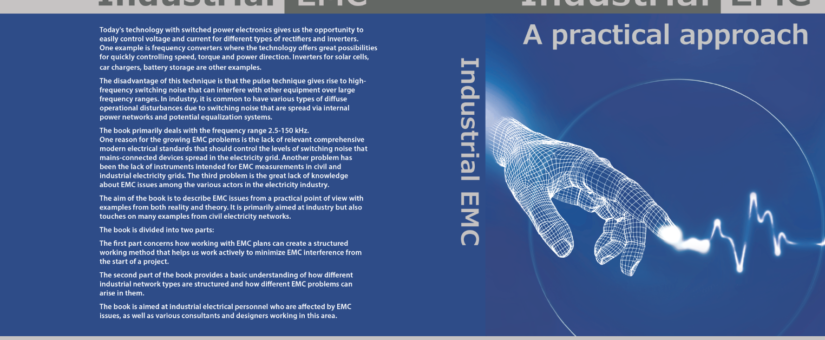
„Industrial EMC – a practical approach” by Reidar Gustavsson
- Posted by Neo Messtechnik
- On 4. July 2025
- 0 Comments
- Industrial EMC - Practical guide for industry, Inspection, testing
Workflow for EMC planning at revamping/new construction in the industry
Developing a plan to manage electromagnetic compatibility (EMC) in a large process industry involves identifying potential sources of electromagnetic interference (EMI) and implementing measures to mitigate their effects. Below are some general steps for creating an EMC plan:
- Understand EMC standards and regulations: Familiarize yourself with the relevant national and international EMC standards and regulations that apply to your industry. This includes standards such as the IEC 61000 series and local regulatory requirements.
- Identify Potential Sources of EMI: Conduct an assessment to identify potential sources of electromagnetic interference within your process industry. These may include electrical equipment, machinery, power lines, wireless communication systems, and other equipment that operate with switched power supply. This refers to everything from smaller power supplies to frequency converter drives in the MW class!
- Reference measurements: When rebuilding an existing facility, reference measurements of interference levels in relevant supply points are necessary to identify potential interference problems before constructing the new process part. These measurements must be sent to the new equipment supplier. This should preferably be done at the initial project stage so the supplier can adapt the design to interference levels in the existing supply and/or airborne interference. Airborne interference refers to strong magnetic fields or high levels of radio signals.
The intended feed point should be measured when building a new process section. Then, as per point 4 below, it becomes a matter of assessing potential problems for the new equipment. - Assess EMI Effects: Determine the potential impact of EMI on critical processes, equipment, and systems in the current process. Identify sensitive equipment or processes that may be affected by electromagnetic interference, such as control systems, communication networks, measuring devices, and safety systems. For revamping in an existing facility, the assessments are carried out based on the results of reference measurements in point 3.
- EMC Thresholds Plan: Establish specific EMC levels and criteria to ensure that critical equipment and processes function properly. This means setting limits on acceptable levels of electromagnetic interference and defining the required immunity levels for sensitive equipment. The user is required to carry out this part precisely in SS EN 61800-3. It is essential for the frequency range 2-150 kHz.
- Identify appropriate measures to minimize interference: Develop a set of measures to mitigate the effects of EMI. These may include implementing appropriate shielding techniques, grounding and bonding methods, surge protection devices, electrical power filtering, and electromagnetic interference suppression.
- Design and Layout Considerations: Ensure equipment, control systems, and communications networks are appropriately located and separated to minimize electromagnetic interference (EMI). Consider factors such as cable routing, separation distance, and equipment grounding to reduce the risk of EMI. This refers to, e.g. cable segregation and zoning during construction.
- Factory tests: For larger processes, it is common for new/revamping to perform factory tests on the equipment before delivery. In addition to any other inspection of the equipment, reference measurements of different EMC levels should also be carried out according to the limit values specified in our EMC plan. This is so that any inaccuracies will be identified and rectified before delivery.
- Assembly/installation: During the physical installation of new equipment, it is imperative that we continuously verify that all installation requirements/guidelines from both suppliers and our own are followed to the letter. This is to avoid discovering hundreds of assembly errors during start-up, which can significantly delay start-up and production.
- Perform verification measurements of EMC levels: Perform EMC tests on critical equipment and systems to verify compliance with the level requirements of our EMC plan and verify power quality and EMC standards. When implemented, this requires reasonably normal operating conditions. Note that measurements must be taken even at maximum load to confirm that all requirements are met.
This may mean repeating EMC testing until the buyer takes over the delivered facility. If the various requirements of the EMC plan are not met, the buyer should not approve a takeover until all points of failure have been corrected. - Training: Relevant personnel must be trained during the start-up and takeover phase. This refers to personnel operating and maintaining equipment and systems affected by EMC requirements. The goal is to raise employees’ awareness about the potential impact of electromagnetic interference and the importance of following the EMC plan and not degrading the EMC characteristics of installed equipment during ongoing maintenance.
- Documentation: Maintain comprehensive records of all EMC-related activities, including test reports, equipment specifications, layouts, and any deviations from the EMC plan. Develop a system to document and track any incidents or problems related to electromagnetic interference. This will be a knowledge base for future projects.
- Regular update: Review and update the EMC plan regularly to incorporate technological developments, regulatory changes, and lessons learned from past experiences. Keep updated with new EMC technologies and methods to ensure continuous compliance with standards and regulations.
See also the book “Industrial EMC ” from NORBO KraftTeknik AB. The book provides an in-depth review of the above points, and much more.
0 Comments